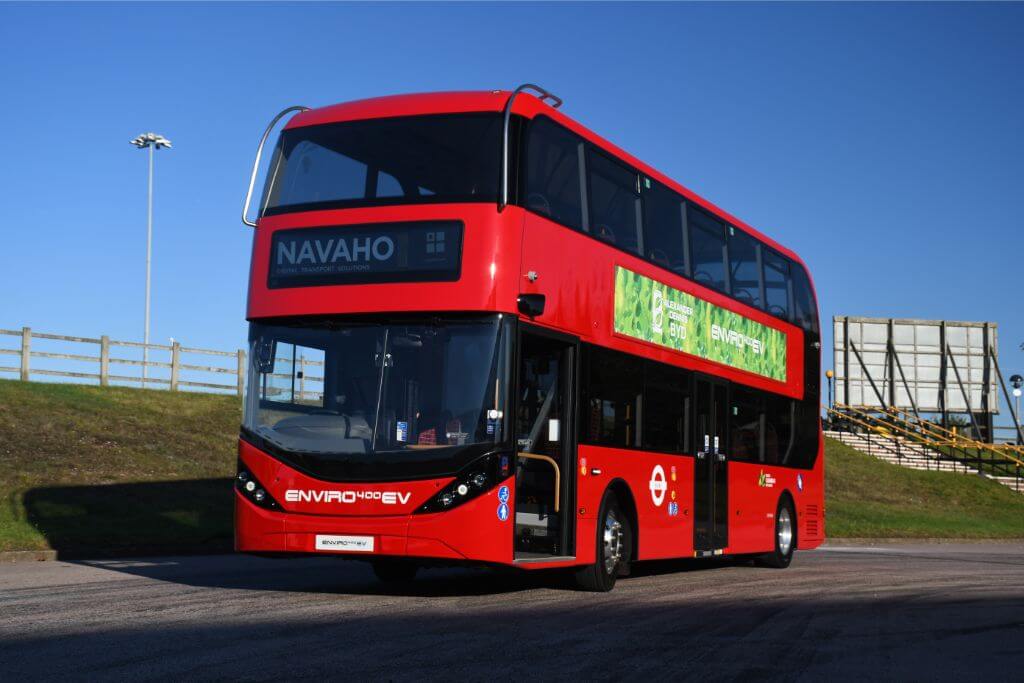
What Go-Ahead London Chief Engineer Chris McKeown enjoys most about his job is the fast pace and varied challenges. He shared part of his day with Andy Izatt recently to give him an insight into what it’s all about
Chris McKeown is Chief Engineer of Go-Ahead London with a fleet of around 2,300 vehicles. Working in a competitive, tendered market where maximising vehicle availability is critical, he is taking a multifaceted approach to delivering that. Not only is he looking for better coordination between different disciplines within his department, he’s harnessing the latest technology to deliver accurate up to date information that can help minimise the time and cost of vehicles off the road.
[…]
By subscribing you will benefit from:
- Operator & Supplier Profiles
- Face-to-Face Interviews
- Latest News
- Test Drives and Reviews
- Legal Updates
- Route Focus
- Industry Insider Opinions
- Passenger Perspective
- Vehicle Launches
- and much more!