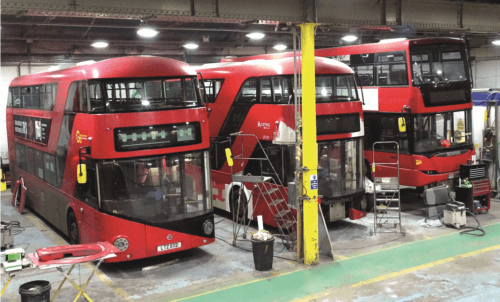
Refurbishing buses is big business. A mid-life refresh can add years to a vehicle’s in-service life. Richard Sharman takes a look behind the scenes to see how the work is carried out at Hants & Dorset Trim, and at a special project that is currently underway
If I said to you Eastleigh, what would you instantly think of?
A town near the city of Southampton? The home of three major bus operators? Or would it be that it is the home of Hants & Dorset Trim? I am pretty sure that most industry people would know it as the place where they have sent their buses to for over 30 years, and within a few short weeks receive them back looking shiny and new.
The mission statement at Hants & Dorset Trim is ‘to provide a simple, honest, on-time, quality service, ensure our customers receive a consistently good service, ensure that there are effective lines of communication with our customers at all times and to lead the way in change, always looking to add value and provide innovative solutions.’ One man is charged with making all that happen, and that is industry stalwart and General Manager Dave Clack.
[…]By subscribing you will benefit from:
- Operator & Supplier Profiles
- Face-to-Face Interviews
- Lastest News
- Test Drives and Reviews
- Legal Updates
- Route Focus
- Industry Insider Opinions
- Passenger Perspective
- Vehicle Launches
- and much more!