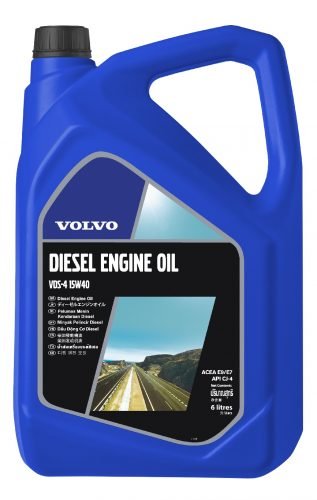
Richard Simpson explains how lubricant developments are advancing in parallel with engine technology
The standardisation of Euro 6 emissions control measures to include SCR and PM filtration, plus, for the majority of engine manufacturers, at least some exhaust gas recirculation, has increased demands on engine lubrication, but also has the potential to allow some fleets to rationalise the different grades of engine oils that they previously had to hold in stock.
For many decades, lubricant blenders providing oils for heavy-duty diesel engines have had to allow for an increasing burden of soot to be carried in suspension in the oil rather than being blown out in exhaust gas, and the introduction of Exhaust Gas Recirculation (EGR) has done nothing to decrease this requirement.
There’s also now an additional soot-related factor to take into account[…]
What you get with a subscription
- Operator & Supplier Profiles
- Face-to-Face Interviews
- Lastest News
- Test Drives and Reviews
- Legal Updates
- Route Focus
- Industry Insider Opinions
- Passenger Perspective
- Vehicle Launches
- and much more!