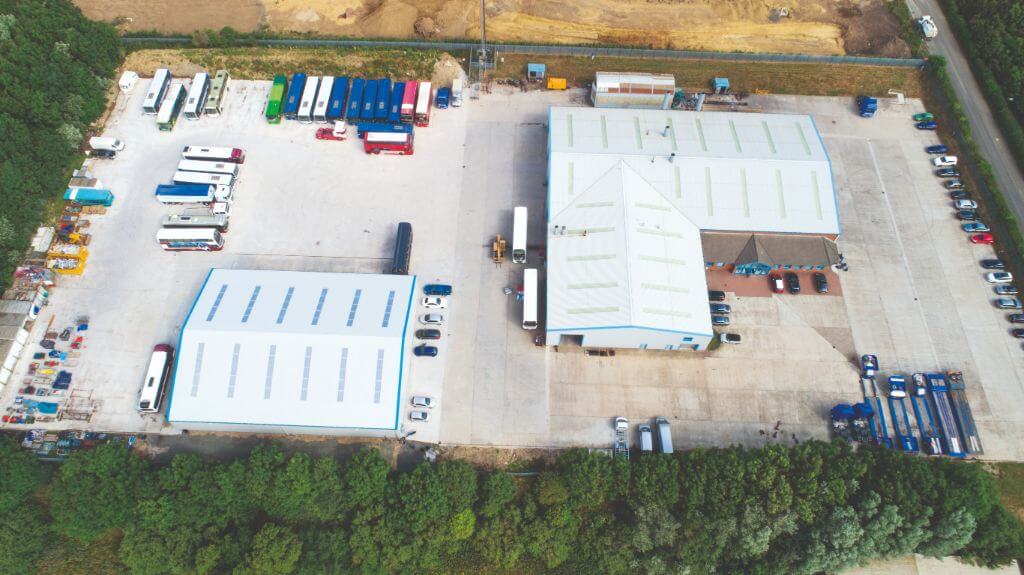
Instead of sitting idly by and watching its bus refurbishment work dry up during the pandemic, Thornton Brothers decided to diversify and begin offering PSVAR conversions. As Peter Jackson found out, that decision turned out to be a fantastic one
Covid-19 has had a huge impact on coach and bus operators, in many cases forcing them to totally reinvent themselves and find new ways of bringing in the cash. For coach operators whose bread and butter was once tour work and day excursions, rail replacement services have become a critical source of revenue. There’s only one catch: you need a PSVAR-compliant vehicle now to win the work.
[…]
By subscribing you will benefit from:
- Operator & Supplier Profiles
- Face-to-Face Interviews
- Latest News
- Test Drives and Reviews
- Legal Updates
- Route Focus
- Industry Insider Opinions
- Passenger Perspective
- Vehicle Launches
- and much more!