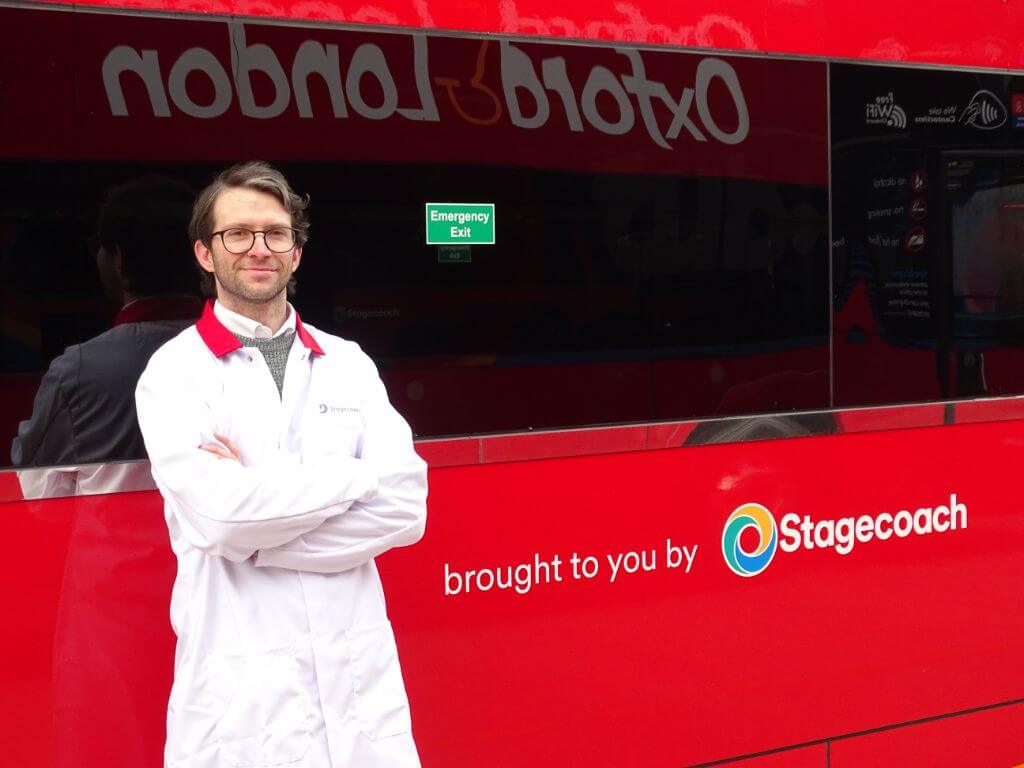
Fleet Engineer Robert Betterton embarked on his new role at Stagecoach a year ago. Richard Sharman found out how that new role quickly changed into one of the biggest challenges of his career due to the pandemic
We have all been there – starting a new job, getting to know your colleagues and how the business works. That is the situation that Stagecoach in Oxford Fleet Engineer Robert Betterton thought he was going to be in this time last year. Weeks later the UK became the latest victim of the pandemic, the country entered a national lockdown and things rapidly changed, with new challenges to be met on both the engineering and cleaning side.
[…]
By subscribing you will benefit from:
- Operator & Supplier Profiles
- Face-to-Face Interviews
- Latest News
- Test Drives and Reviews
- Legal Updates
- Route Focus
- Industry Insider Opinions
- Passenger Perspective
- Vehicle Launches
- and much more!