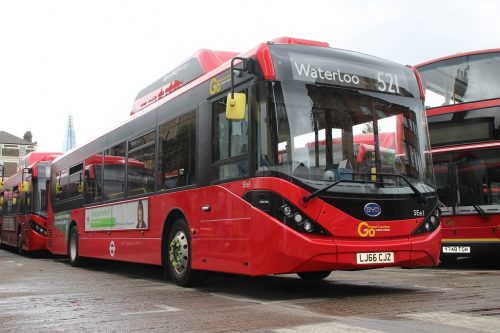
A year since Go-Ahead London’s Waterloo Garage was electrified, Gareth Evans test drives a BYD ADL Enviro200EV along a section of the 521 route
Introducing any new technology almost inevitably brings with it an element of risk – particularly so when that includes the implementation of a new bus type, changing the method of propulsion, new infrastructure and communicating all that with stakeholders, including staff, neighbours and customers. That in a nutshell, is what Go-Ahead London did when it converted Waterloo Garage’s allocation of diesel-powered Mercedes-Benz Citaro buses to electric BYD ADL Enviro200EVs.
The project is one that CBW has followed and featured with interest over the last couple of years – and now it was time to expereince the buses behind the wheel, as well as gain insight for other industry professionals considering following in Go-Ahead London’s footsteps in introducing electric traction.[…]
By subscribing you will benefit from:
- Operator & Supplier Profiles
- Face-to-Face Interviews
- Lastest News
- Test Drives and Reviews
- Legal Updates
- Route Focus
- Industry Insider Opinions
- Passenger Perspective
- Vehicle Launches
- and much more!
Watch Gareth’s Test Drive here: