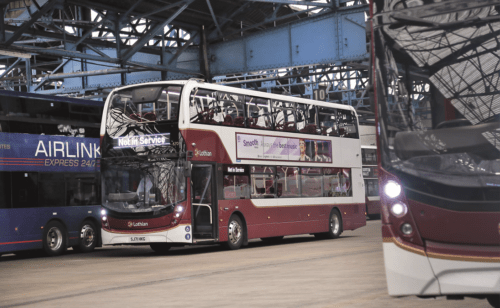
Jonathan Welch speaks to ALBUM host Lothian Buses about its engineering apprenticeship scheme
There has been a lot of focus of late on driver recruitment and how to overcome the shortage across the industry, but it’s important not to forget that the bus industry is more than just its drivers. Behind the scenes, engineers are vital to ensuring that buses are turned out for service every day, especially at an operator like Lothian which prides itself on the smart fleet it is known for. And those engineers just don’t appear by magic, or walk in off the street ready-qualified to maintain everything from seats to suspension.
In an age where vocational training seems to have become the poor relation when it comes to school leavers’ perception versus an academic progression to university, it feels like apprenticeships are slowly regaining a foothold, especially as the bus industry starts to get to grips with the new challenges that decarbonisation brings, and the new skill-sets that go hand in hand with it. We sat down with Lothian’s Engineering Director Colin Barnes and Chief Engineer Dylan Dastey to hear more about how the company is working to ensure it has the right people with the right skills and right aptitude to keep its legacy fleet on the road as well as turn the corner with new technology.
[…]By subscribing you will benefit from:
- Operator & Supplier Profiles
- Face-to-Face Interviews
- Lastest News
- Test Drives and Reviews
- Legal Updates
- Route Focus
- Industry Insider Opinions
- Passenger Perspective
- Vehicle Launches
- and much more!