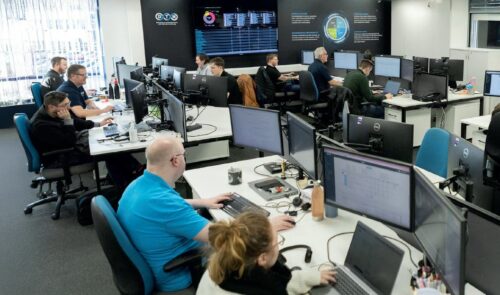
With 20 years of fleet experience, tyre management provider DTM tells us how data from its cloud-based customer portal is providing invaluable insight to inform fleet strategies and support operational objectives
For coach and bus fleet operators, the top priority will always be the safety of passengers, drivers and the public, fulfilling obligations to transport passengers safely whilst meeting daily schedule requirements.
Tyre-failings will have serious consequences, from unplanned downtime leading to a day’s schedule disrupted whilst the Transport Manager deals with a vehicle off the road, to passengers offloaded and your brand associated with the ensuing disruption, to the potentially far more catastrophic outcome of a tyre blow-out leading to a serious collision.
Many of these situations can be avoided with a proactive approach to fleet tyre management. For DTM, this generally begins with analysing a customer’s tyre usage, working practices and brand preferences. This information is then combined with the findings from physical tyre inspections where DTM Fleet Audit Technicians inspect every tyre on every vehicle in a customer’s fleet. This level of detail has proved invaluable to customers and to DTM in providing early warning of tyre issues. Information is uploaded to DTM’s customer portal, enabling essential maintenance to be scheduled and tyre related breakdowns to be averted, as well as providing a history of management information to begin to build an insightful handprint profile for each fleet customer.
Educating and empowering drivers
A valuable finding from fleet audit inspections is driver behaviour, evidenced in tyre wear. At a time when the industry is experiencing a driver shortage and with drivers being highly sought after, it is even more important than ever to support drivers with training, as well as minimising incidents of unnecessary vehicle downtime.
DTM Account Manager Darren Grant tells us: “Tyre tread is like a fingerprint which can provide a great deal of information on driver styles. With coaches and buses, there can be a lot of stop-start which can be accompanied by over-acceleration and wheel spin where we can see spin damage on the tyre. With rural fleets, kerb-related side-wall damage, often on the near side, occurs frequently when the driver comes into the kerb and in their eagerness to get nice and close, they then run the tyre along the side of the kerb, creating expensive and unnecessary damage. By identifying these patterns of driver behaviour, we can use our driver training sessions to promote safer and better driving practices and reduce unnecessary tyre wastage. We can also educate drivers on what to look for in their daily walkaround checks, which again will minimise roadside issues and equip drivers to make the right decisions.”
Maximise tyre life, minimise waste
Fleet Audit Technicians can also arrange for tyre husbandry procedures to be carried out, including regrooving, re-treading and rotating tyres. This proactivity prolongs the life of tyres, ensuring that an otherwise good quality tyre meets its full value, whilst reducing waste and supporting fleet decarbonisation goals.
DTM’s CEO Leigh Goodland says that this approach is fundamental to both DTM’s, and customers’ Environmental, Social and Governance (ESG) commitments. “We have developed a strategy for our business that puts environmental consideration at the forefront of decision making. For our customers, this means that we continue to deliver the best possible services, whilst also reducing the number of tyres used across the year and in doing so, lowering their carbon impact.
Efficient, proactive tyre maintenance can avoid nearly-new tyres being wasted, when the damaged area could be repaired and the tyre-life prolonged, which would reduce operating costs and lessen the environmental impact. This proactive maintenance now plays an important part in our tyre management process and is working extremely well for our customers. When a tyre does reach the end of its useful life, we are partnering with industry specialists to streamline the casing collections process and maximise tyre recycling, to minimise environmental impact.”
Net Zero with EV
Efficiency in tyre management is an essential part of achieving Net Zero goals, and in DTM’s case, the audit trail provided by their customer portal is essential in evidencing a reduction in carbon footprint. Fully electric fleets are providing new challenges in tyre management, as the weight of a coach or bus is increased with the addition of battery weight, which increases the stress on the road surface. EV tyres are designed to reduce rolling resistance which is important to maximise EV range and increase tyre efficiency. DTM is manufacturer-independent and whether for an EV or other fuel type vehicle, will recommend the best suited tyre for the workload of the vehicle, often running tyre tests to substantiate tyre selections.
Insight not hindsight
By analysing tyre use and the effects of driver behaviour, and by implementing
a proactive maintenance approach, tyre performance is optimised and tyre related incidents can be minimised. For coach and bus operators, this is a compelling case for increasing road user safety, lowering fuel costs and reducing fleet carbon output.
DTM’s approach is delivering tangible results for their fleet customers. For DTM’s Darren Grant, with career experience in the coach and bus sector, these preventative actions provide a full service solution. “Our proactive approach with tyres and wheels removes avoidable incidents, and when a fleet customer needs maintenance work, they can book using our on-line portal, or call us and we’ll manage everything. It’s a one stop shop 24/7/365.
You won’t go around the houses. We’ll make all the arrangements with our UK and European partner network, and you receive confirmation. If your vehicle is at the roadside, your driver will receive updates to enable them to communicate with passengers, which takes the pressure off the driver. Everything is tracked
and reported to evidence and support compliance. Reporting enables you to view your spend, and view remedial maintenance at vehicle and depot level to identify high damage areas. It provides total visibility and continuity, which is very exciting for our customers.”