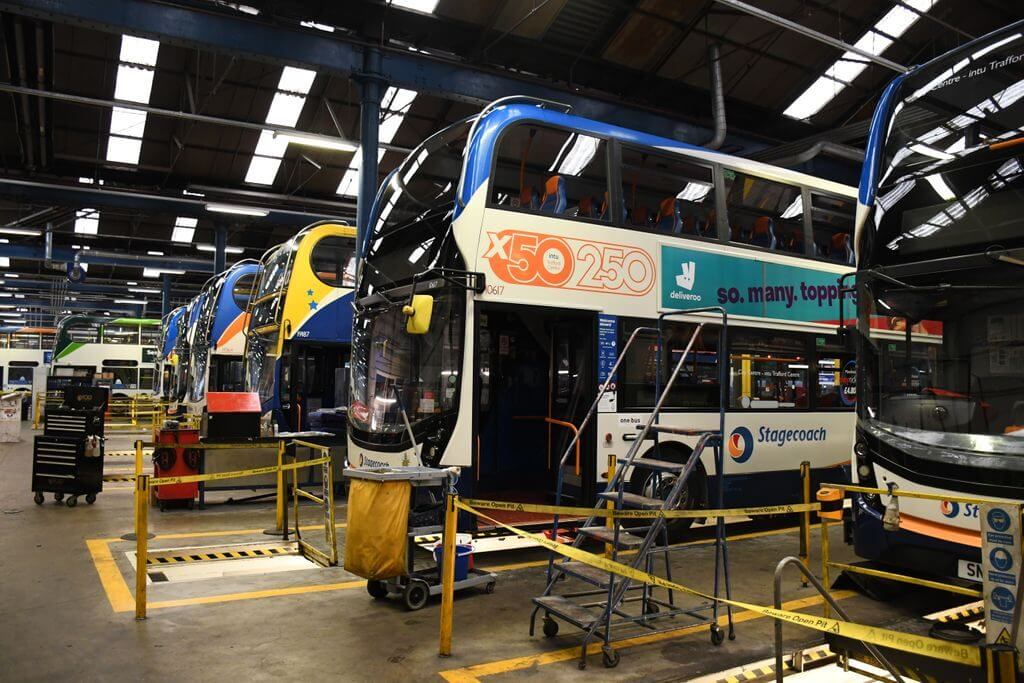
Stagecoach Manchester Engineering Director Peter Sumner has worked in the industry for almost half a century. As he explained to Andy Izatt, experience has taught him that detailed analysis of every aspect of his operation brings the insight he and his staff need to deliver a value for money engineering function
Stagecoach Manchester Engineering Director Peter Sumner has been appointed Operations Engineer for Stagecoach Group from 1 August.
“My new job will be to provide support for the Engineering Directors,” explained Peter. “Since becoming Engineering Director at Stagecoach East Midlands in 1993, I have been heavily involved in the restructure and modernisation of the engineering functions of the companies I have worked for in order to meet the challenges of a deregulated market.
“Since 2011 I have been instrumental in implementing the Stagecoach preventative maintenance programme (Proactive Maintenance) to meet the ever-changing complexities of the fleet. At Stagecoach Manchester I’ve set up audit and KPI monitoring systems to be able to quickly identify areas that are not performing as they should and some of those systems and procedures are now used throughout the Group.
[…]
By subscribing you will benefit from:
- Operator & Supplier Profiles
- Face-to-Face Interviews
- Lastest News
- Test Drives and Reviews
- Legal Updates
- Route Focus
- Industry Insider Opinions
- Passenger Perspective
- Vehicle Launches
- and much more!