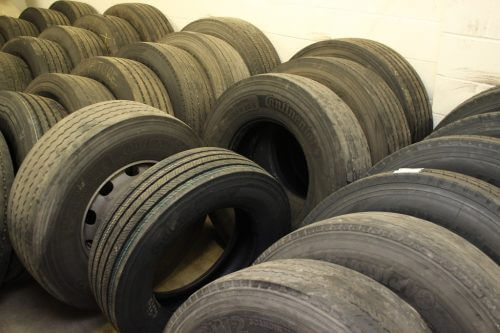
Premium manufacturers are switching from tyres as a product to tyres as a service, while less-established brands are fighting to raise the quality of their offerings. Richard Simpson asks which is the right approach for your operations
The replacement tyre market for coach and bus fleets is undergoing a revolution. For many years, operators fell into two distinct categories: there were big fleets which used premium tyres, and small fleets which used whatever their local stockists could sell them at an affordable price.
Tyre supply to the very biggest bus fleets was dominated by one manufacturer: Michelin; and in many ways the bus industry was a pioneer for the rest of road transport (including the freight sector) because Michelin has routinely supplied bus tyres on a ‘pence per mile’ basis and had staff embedded in operator depots who managed the maintenance, repair and replacement of tyres without the operator’s direct involvement for many decades. This has started a trend now being driven by premium tyre manufacturers across the heavy vehicle industry of supplying tyres as a service priced on use, rather than a utilitarian consumable product.[…]
What you get with a subscription
- Operator & Supplier Profiles
- Face-to-Face Interviews
- Lastest News
- Test Drives and Reviews
- Legal Updates
- Route Focus
- Industry Insider Opinions
- Passenger Perspective
- Vehicle Launches
- and much more!