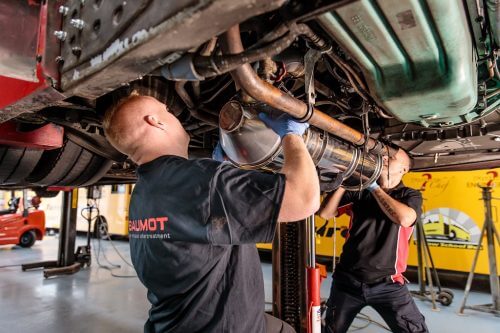
Alan Martin, Customer Relations Manager at Baumot UK, talks to Jade Smith about the company’s BNOx exhaust after treatment system and its new Development and Innovation Centre, which has been established at Silverstone Park in Towcester
The Baumot Group is a leading supplier of exhaust gas after treatment. It offers a broad portfolio of exhaust after treatment systems for retrofit, including original equipment and aftermarket applications. The systems are used in a variety of applications both on-road and off-road.
The Mayor of London, Sadiq Khan, announced plans to retrofit more than half of London’s bus fleet to meet Euro 6 emissions standard by 2020. Following a competitive tender process, five suppliers have been appointed to retrofit the exhaust systems – one of which is Baumot UK.[…]
By subscribing you will benefit from:
- Operator & Supplier Profiles
- Face-to-Face Interviews
- Lastest News
- Test Drives and Reviews
- Legal Updates
- Route Focus
- Industry Insider Opinions
- Passenger Perspective
- Vehicle Launches
- and much more!