Today’s cost-conscious environment continues to focus attention on the need to reduce vehicle operating costs, says Imperial Engineering. As a result, PSV maintenance managers face the challenge of maximising the service life of components in core vehicle systems such as braking, while minimising replacement costs without compromising on safety or performance.
Although pneumatic disc brake systems on buses have been the norm for some time, a number of manufacturers, including Alexander Dennis, Scania, Volvo and Wrightbus, have introduced electronic braking systems (EBS) that incorporate electronically-controlled air brake valves to the braking system. Manufactured by Knorr-Bremse and Wabco, EBS integrates the functions of braking control, anti-lock braking (ABS) and traction control (TCS or ASR) into a single system. Compared to conventional pneumatic control, EBS offers the advantages of reduced braking response time and shorter braking distances.
EBS functions via an electronic control signal from the brake pedal that is processed in an electronic control unit (ECU) and then delivered to the system’s pressure control modules with virtually no time delay. The pressure control modules pneumatically adjust the brake pressure in the brake chambers and simultaneously sends signals from wheel sensors back to the ECU. EBS also helps to reduce wear in the brake system’s components by electronically adjusting the specific braking force needed for each braking situation. The ECU also collects and stores data, enabling the monitoring and maintenance of the system.
While EBS components are designed to last the typical 15-year lifespan of a vehicle, providing they are properly maintained, PSV parts distributor Imperial Engineering says it has seen demand increase for replacement items such as EBS modulators and footbrake modules. Until recently, operators committed to only using OEM parts on their vehicles had no option but to purchase a new OEM component. However, in a welcome move for operators under pressure to reduce costs, Knorr-Bremse and Wabco also offer genuine OEM remanufactured EBS components through their respective Reman Solutions and EconX programmes.
Costing around 20% less than new equivalents, genuine OEM remanufactured EBS components provide operators with a viable alternative without compromising on system functionality, safety or warranty protection. It is important to note that genuine OEM remanufactured EBS components are designed to be remade only once and possess a shorter service life than their brand new equivalents.
This is also a crucial difference compared to other non-OEM remanufactured products on the market that are not subject to the rigorous OEM remanufacturing process and therefore do not offer the same level of quality assurance as their OEM equivalents. For example, the remanufacturing of Knorr-Bremse’s EconX EBS control modules follows similar processes to the production of its brand new equivalents and, in some instances, are built on the same assembly line. They use the identical internal components and are subject to the same end of line tests and quality checks carried out on a brand new product. For OEM remanufactured EBS modules, this involves over 90 individual testing and measurement steps.
As well as offering operators a cost advantage, OEM remanufactured components are also more sustainable. Remanufacturing conserves resources and consumes much less energy, reducing CO2 emissions.
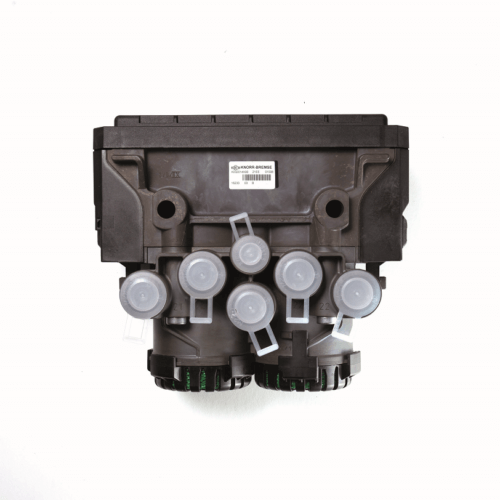