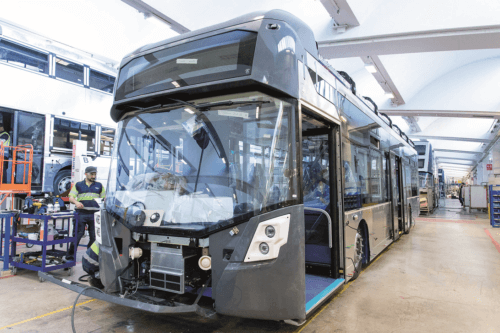
Jonathan Welch paid a visit to the Wrightbus factory to see what goes in to producing the firm’s diesel, electric and hydrogen-fuelled buses
From its early days as a small Northern Irish specialist vehicle manufacturer, Wrightbus grew to be one of the biggest names in the UK bus market in just a few decades, becoming a staple provider to FirstGroup, as well as a myriad of other, small and medium sized companies across the country and in the Far East. The troubled period of the late 2010s is well documented, as is its sale out of administration to JCB heir Jo Bamford in 2019. Just three years later, the company has re-established itself and is on a firm footing to move into the era of zero-emission buses, continuing the pioneering spirit of innovation of its founder, the late Sir William Wright.
In mid-November, the growing manufacturer took on it’s 1,000th employee, marking a significant milestone for the firm as it re-establishes itself both as a manufacturer and major local employer, and follows what the firm describes as an ‘outstanding year’ in which it has secured a series of high-profile deals in the UK and overseas, and launched a new sister company, AllServiceOne, which offers repair and maintenance to operators of all vehicles, not just Wrightbus products.
Building on work which had already been started prior to administration, sales of its zero-emission buses have risen from none when Jo Bamford took over, to 50% of production in 2022. Wrightbus’ Hydroliner hydrogen buses, in service in Aberdeen, Birmingham, Dublin and London, have covered over 1.5 million miles since first entering service, preventing an estimated 2,366 tonnes of CO2 emissions entering the atmosphere compared to journeys made by an equivalent diesel bus, the same as removing around 550 cars from British roads for a year. The battery-electric Electroliner is also becoming more common, including with Translink in Belfast, Transport for Ireland and Abellio in London.
Proud
Jo Bamford has said he is ‘immensely proud’ of how far the firm has come in the first three years under his stewardship, and of the contribution it was making to the UK economy and net zero ambitions. “When I took over the company, I was clear about my ambitions for it, both in terms of contributing to the UK’s plans for net zero and in terms of supporting the British economy,” he said. “We have invested heavily in the last three years and it is remarkable to see 1,000 members of staff now employed in Northern Ireland, when there were just a handful of people left when the company was bought out of administration.
[…]By subscribing you will benefit from:
- Operator & Supplier Profiles
- Face-to-Face Interviews
- Lastest News
- Test Drives and Reviews
- Legal Updates
- Route Focus
- Industry Insider Opinions
- Passenger Perspective
- Vehicle Launches
- and much more!