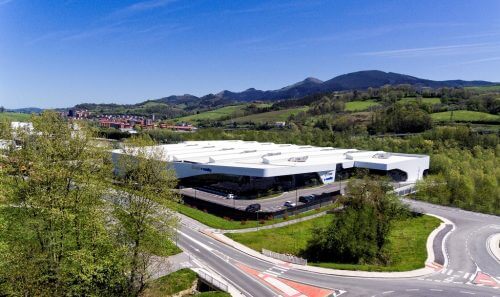
Irizar has officially opened its purpose built e-mobility manufacturing centre in Aduna in the northern Spanish province of Gipuzkoa, and took the opportunity to unveil an unexpected new addition to its electric vehicle range that underlines its commitment to provide customers with one-stop solutions. Andy Izatt reports
Irizar, with an anticipated annual turnover of €700m (2017: €620m) this year, has officially inaugurated its purpose-built e-mobility manufacturing centre in Aduna near San Sebastián in the north Spanish province of Gipuzkoa. Built on a site that is almost four hectares in size and incorporates a dedicated test track, what is described by its creator as the first electromobility plant in Europe represents an investment of €75m. The building itself encompasses 18,000 square metres and with an eye to future expansion, an adjacent similar size plot of land has also been acquired.[…]
By subscribing you will benefit from:
- Operator & Supplier Profiles
- Face-to-Face Interviews
- Lastest News
- Test Drives and Reviews
- Legal Updates
- Route Focus
- Industry Insider Opinions
- Passenger Perspective
- Vehicle Launches
- and much more!