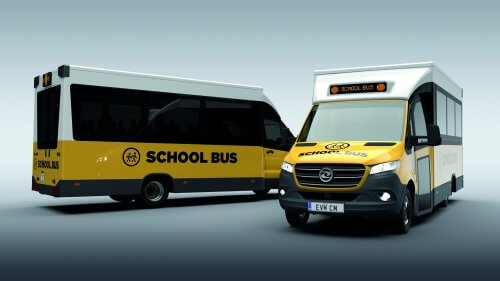
Minibus manufacturer EVM has taken a step to widen its market presence with the introduction of a new composite body structure for the school and accessible transport sectors
Following the recent announcement of low-emission certification and zero-emission drivelines for its range of Mercedes-Benz Sprinter-based minibuses, EVM has announced what it calls a ‘whole new concept for minibus design.’
Targeted at the school and accessible side of the market, EVM believes the composite modular (CM) body will allow it to grow outside its traditional executive segment: “We have enjoyed a steady growth in our presence in the school and accessible market over the last five to six years with our Trend, Elegance and in particular our Cityline model,” explained Peter Flynn, Sales and Marketing Director. “Substantial successes in tendering to Municipals across the United Kingdom have refocussed us on developing solutions specifically for these markets.”
[…]
By subscribing you will benefit from:
- Operator & Supplier Profiles
- Face-to-Face Interviews
- Latest News
- Test Drives and Reviews
- Legal Updates
- Route Focus
- Industry Insider Opinions
- Passenger Perspective
- Vehicle Launches
- and much more!