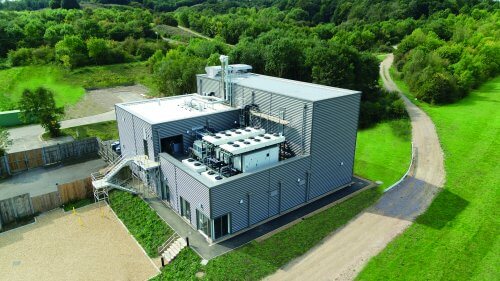
UTAC CERAM Millbrook recently unveiled the successor to its Variable Temperature Emissions Chamber (VTEC). VTEC 2 is so much more than that, though, as Peter Jackson found out
Millbrook is a name synonymous with vehicle testing. Whether it’s the high-speed bowl that first comes to mind, the flowing alpine test track or the merciless Belgian Pavé – all of which have made TV appearances on the likes of Top Gear – the Bedford-based Proving Ground has it all. The facility is even transformed into a film set on occasion – James Bond’s Aston Martin DBS was famously rolled over at Millbrook in a spectacular scene from Casino Royale, released in 2006.
[…]
By subscribing you will benefit from:
- Operator & Supplier Profiles
- Face-to-Face Interviews
- Latest News
- Test Drives and Reviews
- Legal Updates
- Route Focus
- Industry Insider Opinions
- Passenger Perspective
- Vehicle Launches
- and much more!